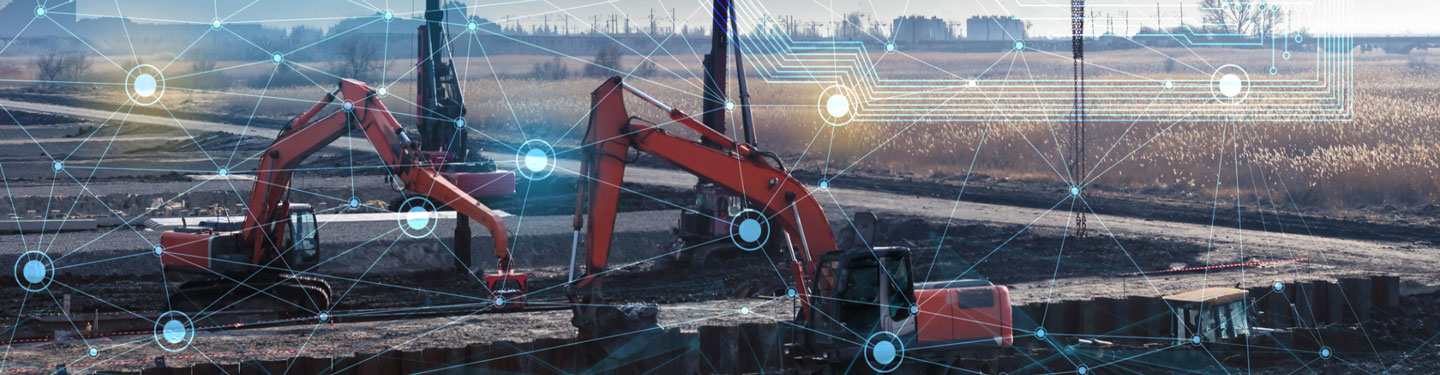
Digital transformation of mining: challenges and opportunities
The digital modernisation of South African mines is a significant shift towards the Fourth Industrial Revolution (4IR) with mining companies creating value and envisioning the future of work as they mature digitally.
According to a 2023 PWC survey, 100% of mining CEOs in South Africa are now committed to transitioning to digital technologies, including the integration of these technologies into their Environmental, Social, and Governance (ESG) programmes. Despite these advancements, the survey reports a consensus among South African mining CEOs that, although there has been development in the use and understanding of technology within the mining sector, there is room for improvement.
Where to start, when, and how much to invest remain debatable questions. Many of South Africa’s conventional mines are old, complicating the hunt for value in digital modernisation. Legacy systems aren’t easily retrofitted, making efforts costly and challenging ROI calculations. If the lifespan of a mine is short, less than seven years, digitalisation and achieving ROI is almost impossible in this already labour- and capital-intensive industry. However, according to Mining Review Africa, digitalisation is nevertheless proceeding across the value chain – from finding and mining through processing and trading. Open pit operations are moving swiftly ahead, with underground mining lagging. A key obstacle here is that the industry faces a global competition for talent, needing to create an environment that attracts not only miners but also data scientists and digital natives.
An eye on the benefits – it’s about the data
Digital tools can drive productivity, improve safety, and ensure environmental stewardship. Automated drilling and hauling systems, Internet of Things (IoT) sensors monitoring mine conditions, drones for surveying, and data analytics for operational efficiency are just some technological possibilities. All depend on extracting value from data – finding, organising, and analysing it, at speed. By centralising operational data, mine operators are able to use the information to improve the condition and functionality of their assets, allow for remote work, and ensure that processes run efficiently.
Digitisation’s potential to enhance decision-making cannot be understated. Real-time data allows for the swift identification and rectification of operational inefficiencies, leading to cost savings and increased production rates. Mine operators can use predictive analytics to anticipate equipment failures before they occur, reducing downtime and maintenance costs. Centralising data management, applying master data management strategies, and using model-driven processes allow for better planning, taking advantage of market prices, and improving recovery forecasts.
Digitisation efforts are currently clustered in processing areas of the business, and in logistics, planning and supply chain management. In these areas, small improvements make a big impact on the bottom line. By digitising work, the Mining, Mineral processing, and Metals industry (MMM) has a quick win in collaboration, productivity, and efficiency. Digital work can be done from anywhere in the plant, from various sites, or remotely. People can accomplish more.
Safety is of course a key issue in the MMM sector, and digitisation offers remarkable tools to protect workers. Technologies such as wearables that alert systems to hazardous conditions can significantly reduce workplace accidents. Labour unions, integral stakeholders in the industry, have also noted that digital technology is vital for improving health and safety, and plays a significant role in communication.
ESG regulatory pressures and the drive to Net Zero are increasing in the MMM industry, with global leaders looking to implement digitisation initiatives. Software applications help to automate and optimise operations, identifying opportunities to reduce energy use. They can also take care of ES-related recording, reporting and data analysis. Asset monitoring can extend equipment lifetime and reduce waste.
Overcoming challenges with strategy and foresight
A Wits study reveals that the journey towards digital transformation in the mining industry requires a strategic map and a clear vision. During the initial stages, it’s essential to build momentum, ensure regulatory alignment, and establish a clear business case to guide the way. As the execution unfolds, the right skills must be in place, the culture aligned with the new digital ethos, and the IT and connectivity infrastructure made robust enough to support the change.
Effective governance is key to steering these initiatives in the right direction. This includes maintaining a progressive vision and ensuring seamless coordination across all levels of the organisation. To clear the path, companies need to work towards convergence of IT/OT systems and data, clarifying roles, fostering a shared vision, and encouraging a culture receptive to change. Addressing regulatory concerns and adapting institutional setups will also be part of the process, especially considering the hesitancy that may come with longstanding practices and the integration of legacy technologies.
The digitisation of South African mining is a story of an industry at the crossroads of tradition and technology, grappling with the challenges of change while eyeing the vast opportunities that lie ahead. Successfully navigating this terrain could make the mining sector’s future brighter, smarter, safer, and more sustainable.