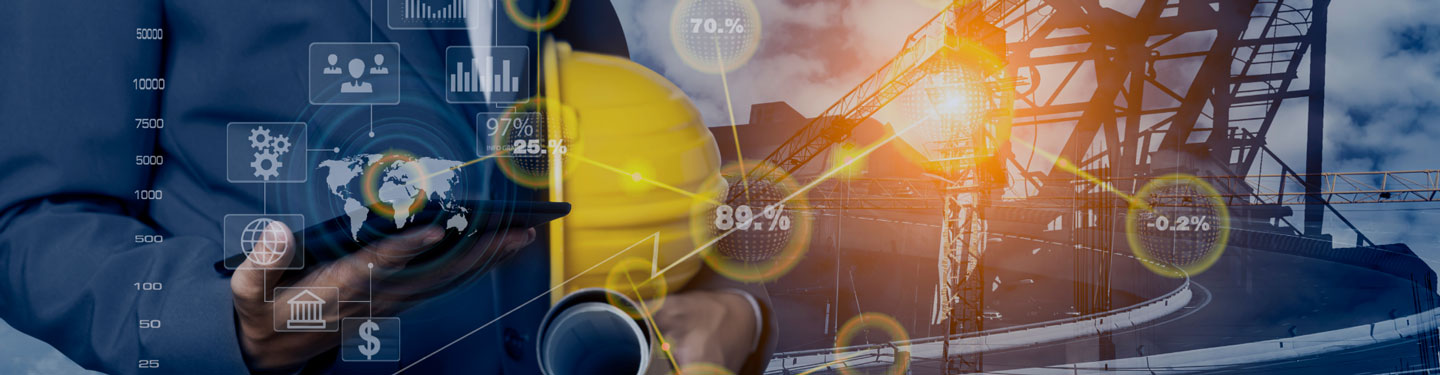
Digital shifts in South African mining: putting people and the value chain in focus
Digital mining in South Africa is no longer a buzzword; it’s a transformative force poised to reshape the sector. By incorporating advanced technologies such as AI, machine learning, and automation, digital mining promises to enhance operational efficiency, improve worker safety, and reduce costs and environmental impacts. However, the integration of these technologies also raises crucial questions about the future of employment and the broader socio-economic implications for a country that still relies heavily on mining.
Technology meets tradition across the entire value chain
The labour-intensive South African mining industry, contributing R361.9bn to GDP and directly employing almost half a million people, is at a critical juncture. The adoption of Fourth Industrial Revolution (4IR) technologies is essential to maintaining competitiveness and attracting investment. These technologies, such as AI and machine learning, could completely change how minerals are extracted and processed, potentially extending mine life, and increasing productivity. But they’re not just tools; the technology is a catalyst for transformation that will redefine how mining operations are conducted. Between 2 and 4 million people depend on the mining sector’s viability, interlinked as it is with numerous other economic sectors. There’s every reason for this shift to come with significant apprehensions, particularly about potential job losses and broader societal impacts.
As digital technologies become integral to mining operations, they are changing every segment of the value chain, from exploration to extraction, processing, and distribution. The promise is increased efficiency and productivity. For example, AI and machine learning can vastly improve mineral exploration and processing, enabling mining companies to identify and extract valuable minerals more accurately and efficiently. Automated and remote-controlled equipment can operate in hazardous environments, enhancing worker safety and reducing the risks associated with deep underground mining. This does not reduce operational costs but could minimise environmental impact.
Digital innovations are also reshaping supply chain logistics. The broader implications of this shift extend to the related industries and communities. By improving efficiency and reducing costs, digital mining can potentially lower the prices of raw materials, benefiting downstream industries and consumers. However, this transition also raises concerns about job displacement, necessitating a proactive approach to workforce development and community engagement to ensure a balanced and equitable advancement of the sector.
4IR: From threat to opportunity
The mining sector’s contribution to GDP is declining, indicating a pressing need for transformation, especially to mine South Africa’s deep-level complex ore bodies profitably. The challenge lies in balancing technological advancement with workforce sustainability.
A recent McKinsey cross-sector analysis does not see digitisation and job losses as automatic companions. It suggests that digitisation could lead to a net gain of 1.2 million jobs in South Africa by 2030. But, say their analysts, businesses need a strategic action plan to leverage these opportunities. The plan needs to include investing in reskilling and upskilling their workforce, ensuring employees transition to new roles that demand new skills. No doubt, technology will create, is creating, new kinds of jobs, but it’s incumbent on MMM industry leaders to prepare their workforce for these changes with training and career development interventions geared to future demands.
There seems to be cautious recognition of these imperatives by mining unions. The Minerals Council of South Africa stresses a ‘people-centric’ approach to 4IR, focusing not only on technological advancement but also on enhancing work culture, and upskilling workers. This perspective is aligned with the unions’ people-centric stance, emphasising the importance of creating safer, healthier, and more fulfilling jobs in the wake of technological changes. The hope is that digital mining can become an opportunity rather than a threat, if managed proactively. Government has a role in mitigating the impact of automation-related job losses. Here, investing in strengthening STEM (Science, Technology, Engineering, and Mathematics) subjects, especially in primary schools, and investing in vocational training are critical in preparing the workforce for the digital era.
Navigating the digital future
The digital shift in South African mining is not just about technology; it’s about putting people and the entire value chain in focus, ensuring a sustainable, prosperous, and inclusive future for the mining sector. Whilst there are concerns about job losses, including the possibility of 200 000 job losses by 2030 if current (non-digital) trends continue, the integration of 4IR technologies could extend the life of mines and create new employment opportunities. To successfully navigate this transformation, a collaborative approach is essential, where government, industry, and educational institutions work together to harness the full potential of digitisation.